El marcapasos en un sistema productivo es lo que nos definirá cuándo debemos fabricar. Nos da la información del cliente y, dependiendo dónde lo situemos, nos definirá el plazo de entrega, la configuración del sistema de información de nuestra fábrica y el nivel del stock necesario.
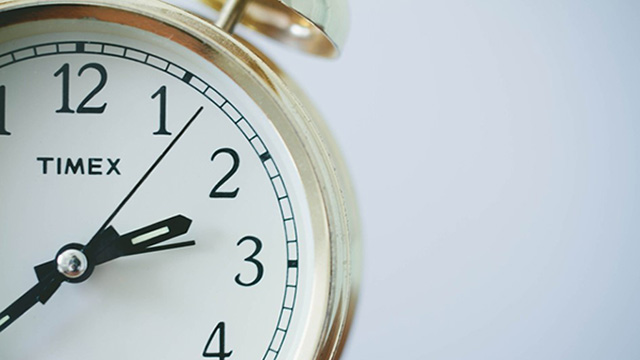
Qué entendemos por Marcapasos en un sistema productivo
El marcapasos en un sistema productivo (pacemaker en inglés) es el sistema que nos definirá cuándo debemos fabricar un producto. Esto es, cuando un cliente ha realizado una compra.
Es importante asegurar que esta información, en un entorno Lean, se deberá «inyectar» en un sólo punto. Es decir, no hay que enviarla a diferentes áreas productivas. Si fuese así, estaríamos volviendo al sistema de producción empujada (push), con los problemas que ello implica. A partir de ese punto, comienza a trabajar mi sistema para reponer o producir lo que el cliente nos pide.
Aunque tengamos una cadena de valor larga, vamos a ver que no es tan complicado definir cuál es el lugar más conveniente para ubicar el marcapasos. En cualquier caso, dependerá fundamentalmente tanto de la variedad de artículos que tengamos, como del plazo de entrega requerido por el cliente.
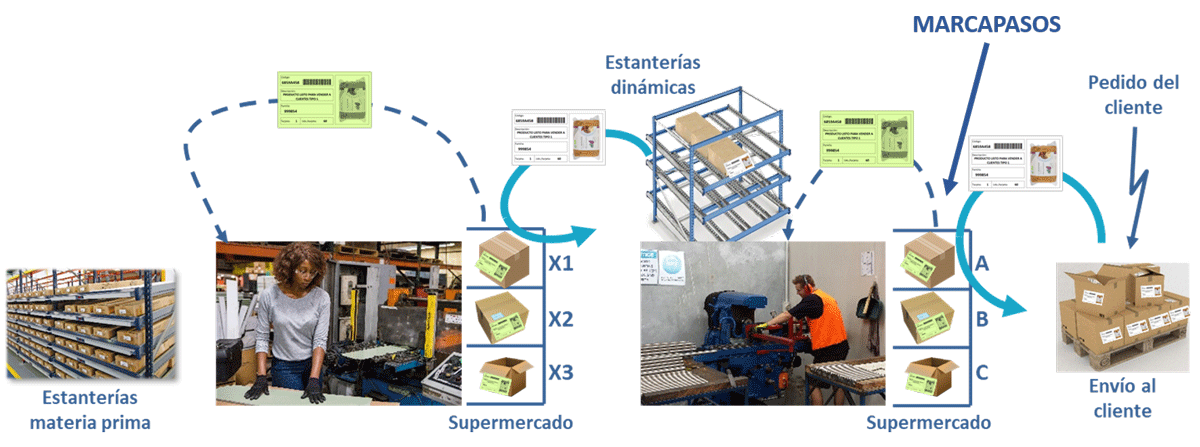
Ahora que sabemos el beneficio del marcapasos, ¿dónde lo ponemos? ¿Al principio, al final o en medio?
Ventajas e inconvenientes al final de la cadena
El marcapasos se encontrará en el punto en el que el cliente recibe el producto que necesita. Al estar al final de la cadena, en el caso de que se requiera entrega inmediata, el producto ya está disponible, y a la espera de que nuestro cliente se lo lleve.
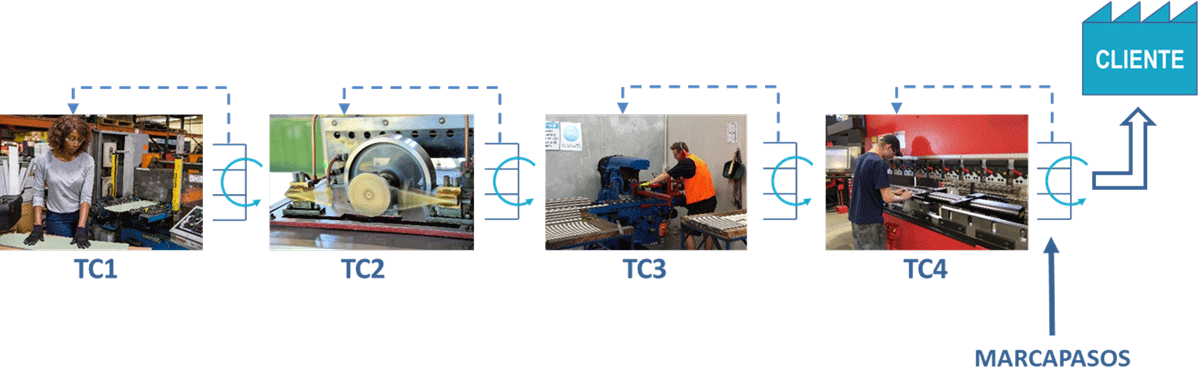
Nota. Este sistema se basa en un Kanban, de forma que el cliente retira el producto deseado, y el kanban transmite la información al proceso anterior para que se reponga. Asimismo, al consumir materiales para producirlo, se generarán nuevos kanban en el proceso aguas arriba sucesivamente. Así es como ponemos en marcha toda la “maquinaria” para reponer el producto consumido.
Para que esto funcione, debemos tener stock de todos estos artículos gestionados por kanban. Si nos imaginamos que hay una gran variedad de productos para nuestros clientes, y para su fabricación una gran variedad de artículos (materias primas y semielaboradas), necesitaremos mucho espacio para almacenarlo todo. Además todo este stock generará grandes inconvenientes, como por ejemplo, mayor espacio en planta, más recursos en logística, mayor gestión, aumento del inmovilizado, problemas potenciales de calidad, riesgo de obsolescencia, existencia de problemas ocultos, entre otros.
En el caso de tener células de producción, se verán enormemente penalizadas por este exceso de stock, llegando a perder algunas de los beneficios para los que fueron diseñadas y construidas.
Por lo tanto tiene sentido tener el marcapasos al final de la cadena en el caso de que la variedad sea limitada en todas las fases de la cadena. De esta manera los supermercados tienen todas las referencias para suministrar a los diferentes puestos productivos intermedios, o enviar el producto final al cliente.
Ventajas e inconvenientes si lo ponemos en un punto intermedio de la cadena
Para ello consideremos que en nuestro ejemplo el marcapasos se encuentra en el segundo proceso de la cadena. Si es así, a partir del momento que un cliente necesite un producto, se deberá procesar el producto en todas las fases desde ese punto hasta el final. Por lo tanto el tiempo requerido será el tiempo de ciclo del puesto 2, más el del puesto 3 y el del 4. Es decir, el plazo de entrega será la suma de los tiempos de procesado de cada etapa desde el marcapasos hasta el final.
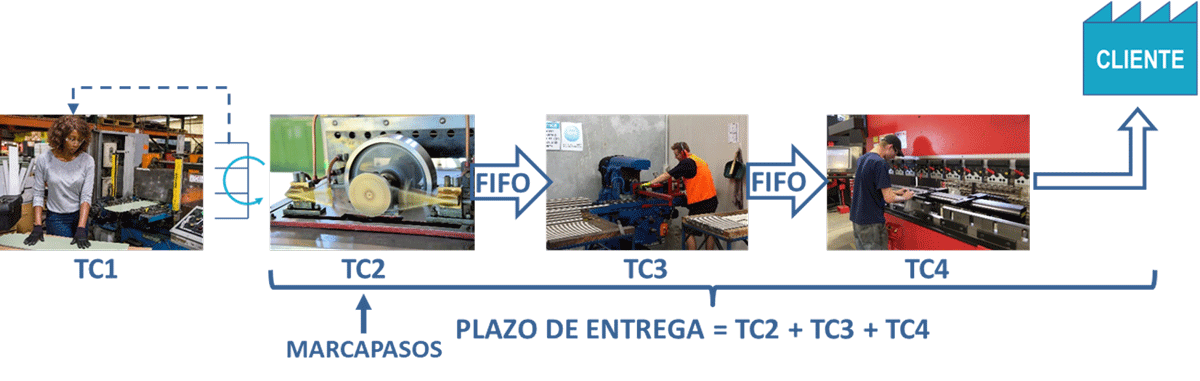
Analicemos qué pasará en torno al punto donde inyectamos la información:
- Aguas arriba del marcapasos, el sistema de gestión será de flujo tirado (pull), por lo que tendremos que disponer de un supermercado inmediatamente antes para poder disponer del material que necesitamos, y así sucesivamente hasta el principio del proceso. Esto aplica para los materiales gestionados por kanban.
- Asimismo, desde el marcapasos en dirección aguas abajo, los productos se producirán en secuencia, siguiendo el orden en el que han empezado, es decir, asegurando el FIFO. Es como si tuviésemos una fila ordenada en la que los artículos van pasando por todas las fases.
Esto será muy útil en los casos en los que tengamos mucha variabilidad o en productos muy grandes, ya que no necesitamos tener stock de todas las opciones, ni el espacio requerido para ubicarlo. Sólo tenemos el stock de lo que se está produciendo en ese momento.
El principal inconveniente que nos podemos encontrar es que el plazo de fabricación una vez recibida la señal en el marcapasos hasta la entrega al cliente sea superior al requerido por éste. Es decir, plazo de entrega demasiado largo.
Ventajas e inconvenientes si lo ponemos al principio de la cadena
Este es el mismo caso anterior, llevado al extremo, en el que únicamente existen procesos aguas abajo del marcapasos.
Ahora nos encontramos con que la gestión y almacenaje de productos semielaborados no existirá, ya que se comenzará la fabricación de nuestros productos desde el principio del proceso.
Al igual que en el caso anterior, la dificultad viene por el hecho de que el cliente no dispondrá del producto hasta que realicemos el proceso completo. Es decir, nuestro plazo de entrega será el tiempo de ensamblaje completo.
Este caso es el utilizado en ventas por proyecto, en las que los productos son únicos, diseñados y fabricados especialmente para el cliente. De hecho, el proceso en la cadena comienza con una fase de diseño y aprovisionamiento, teniendo que considerar en ocasiones también la búsqueda de nuevos proveedores. También se da en los casos de productos especialmente grandes. Existen gran cantidad de ejemplos, como podría ser la construcción de una grúa, un barco, calderas industriales, etc.
Resumen y conclusiones
Por lo tanto ya hemos visto que cuanto más aguas arriba situemos el marcapasos, menor es el stock, pero por otra parte mayor será el plazo de entrega.
No debemos olvidar que un sistema Lean busca, entre otros aspectos, dar una respuesta rápida al cliente. Por lo tanto, la configuración inicial debería situar el marcapasos al final de la cadena. De esta forma la respuesta al cliente será óptima en cuanto a plazos de entrega.
Esta situación no siempre será posible por los factores comentados anteriormente, ya sea por falta de disponibilidad de espacio o gran variedad de modelos, viéndonos obligados a mover el marcapasos aguas arriba en mi cadena. En ese caso encontraremos el punto óptimo, debiendo prestar atención a nuestro plazo de entrega, ya que irá aumentando, y no deberíamos superar al requerido por el cliente.
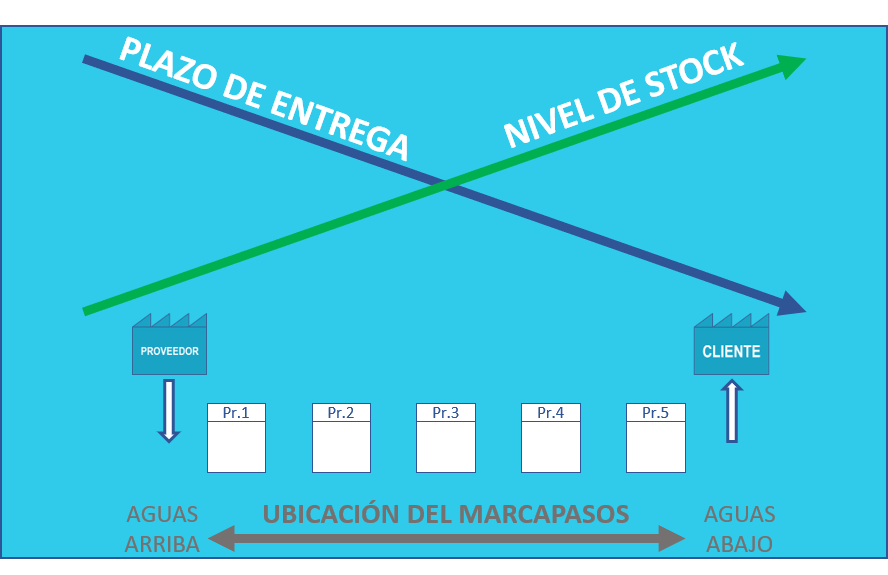
Si este es nuestro caso, tal vez nos encontremos en la necesidad por una parte de disponer stock de producto acabado para dar servicio al cliente, y por otra situar el marcapasos aguas arriba para no tener las penalizaciones de espacio requerido y stock en nuestra cadena.
¿NECESITAS ACOMPAÑAMIENTO PARA PONER EN PRÁCTICA…
Proyectos más habituales que llevamos a cabo: CONSULTORÍA LEAN